Dr.-Ing Jörg Niemeier, ATN Automatisierungstechnik Niemeier GmbH, Berlin
Aufgrund Fachkräftemangels und steigender Qualitätsanforderungen rückt Roboterlöten zunehmend in den Fokus. Anforderungen und daraus resultierende Lösungen sind vielfältig, weshalb verschiedene Lötverfahren zur Verfügung stehen. Die optimale Auswahl kann daher komplex sein.
Kolbenlöten
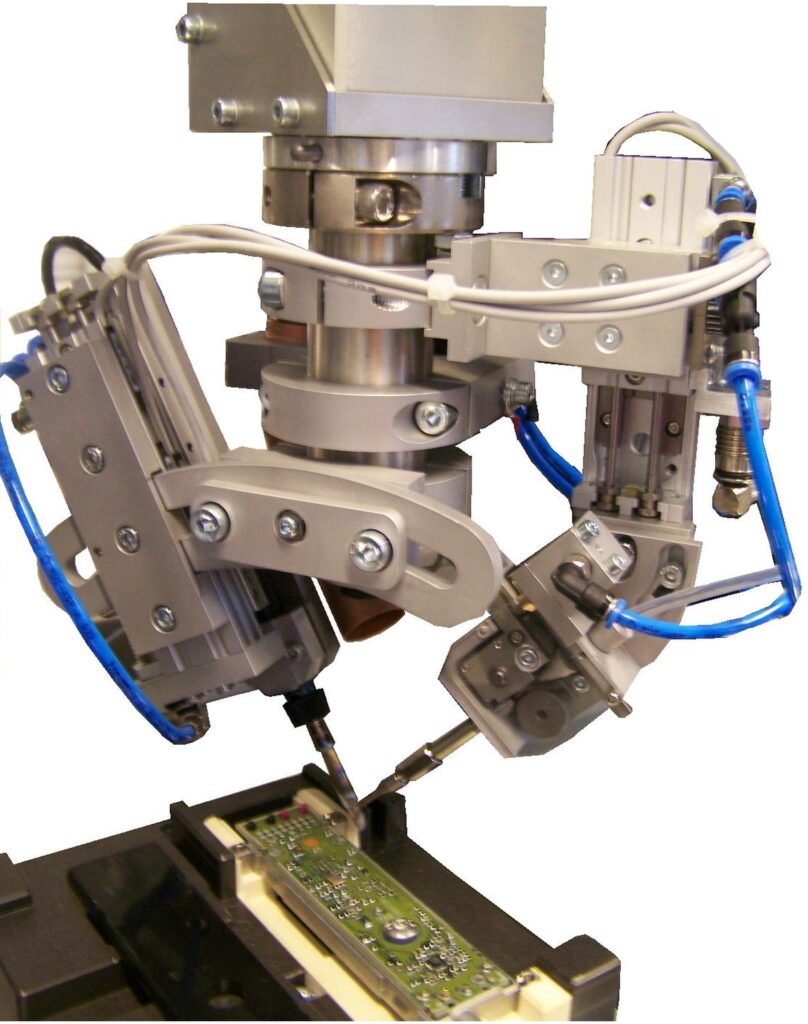
Beim automatisierten Kolbenlöten erhitzt ein elektrisches Heizelement die Lötspitze, die präzise die Lötstelle aufschmilzt. Das Lot wird als Draht zugeführt. Um Oxidationsverschleiß vorzubeugen, wird die Lötspitze mit Nickel oder Eisen beschichtet. Passive Lötspitzen werden auf das Heizelement aufgesetzt. Bei Verschleiß wird nur die Spitze ausgewechselt werden, dies senkt Instandhaltungskosten drastisch. Bei „aktiven“ Lötspitzen ist das Heizelement in die Spitze integriert, was eine bessere Wärmeübertragung und kürzere Lötzeiten ermöglicht. Anders als beim Handlöten wird beim Lötroboter der Kolben immer mit derselben Stelle aufgesetzt. Dies führt zu höherem Verschleiß und verringert die Standzeit. Beschädigungen der Beschichtung können schwerwiegende Folgen haben: Das Zinn löst das Kupfer unter der Eisenschicht und bildet nicht sichtbare Hohlräume, die die Wärmeleitung beinträchtigen. Dies kann zu Lötfehlern führen, deren Ursache ohne Inspektion schwer zu erkennen ist. Trotz Bestrebungen Kolbenlöten durch andere Verfahren zu ersetzen, bietet das automatisierte Kolbenlöten weiterhin Vorteile in puncto Präzision und Effizienz. Die Wahl des Lötverfahrens sollte bereits in der Entwicklung erfolgen und die spezifischen Anforderungen des Verfahrens berücksichtigen.
Laser- und Lichtlöten
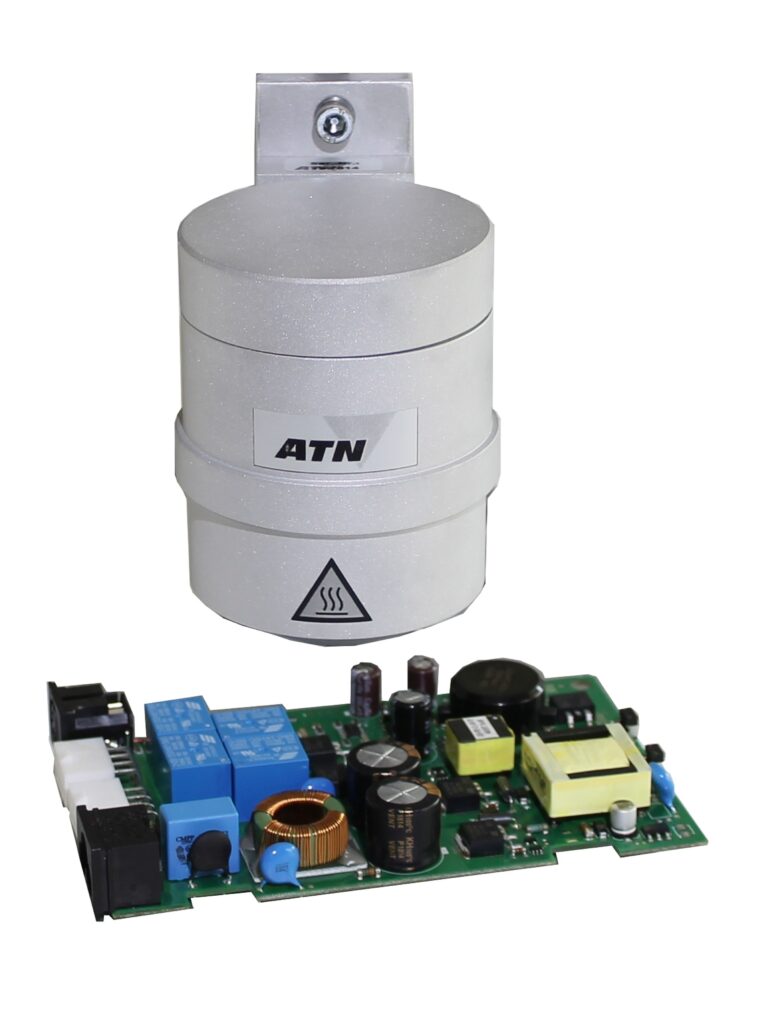
Zum Laserlöten werden überwiegende fasergekoppelte Diodenlaser mit Wellenlängen von 800-980nm eingesetzt. Die Leistung kann über den Strom schnell und exakt einstellt werden, so dass Temperaturprofile realisiert werden können. Das gebündelte Laserlicht wird über ein flexibles Lichtleitkabel und eine Fokussieroptik auf den Bearbeitungspunkt geleitet. Meist wird eine Kamera eingespiegelt. Dabei kann der Strahl geformt werden: neben runden sind auch ovale oder ringförmige Formen üblich. Vereinzelt kommen auch mehrere kleinere Laser zum Einsatz. Dabei ist es schwierig diese exakt zu justieren.
Die Integration von Pyrometern in Laserköpfe ist mittlerweile technologisch möglich, stößt in der Praxis jedoch auf Herausforderungen. Die Messung der Lötstellentemperatur mittels Pyrometer erweist sich als problematisch, da diese Methode erst ab ca. 100° zuverlässige Ergebnisse liefert. Die Erwärmungsphase des Prozesses kann somit nicht erfasst werden. Zusätzlich beeinflussen zwei Faktoren die Genauigkeit der Temperaturmessung, der Emissionskoeffizient(?) und die Oberflächengeometrie. Beide verändern sich während des Vorgangs erheblich: In die glatte, bereits erwärmte Oberfläche taucht der kalte Lotdraht als Störkontur ein und verändert Geometrie und Emissionskoeffizient. Auch beim Löten mit Lotpaste erscheint der Einsatz von Pyrometern fragwürdig. Zu Beginn des Lötprozesses ist die Lotpaste dunkel grau und hat eine körnige Oberflächenstruktur mit ? >0,5. Dann tritt das Flussmittel aus und die Oberfläche wird glänzend. Wenn das Lot schmitzt, entsteht eine hochglänzende Oberfläche mit deutlich geringerem Emissionskoeffizienten.
Neben Systemen mit festen Fokuspunkt können auch flexible Strahlenablenksysteme, sogenannte Galvo-Scanner, eingesetzt werden. Diese bieten zusätzlich zur Fokussierung des Laserstrahls eine schnelle Strahlablenkung, um diesen präzise zu positionieren. Hierbei lenken frei programmierbare Spiegel den Strahl mit Geschwindigkeiten zwischen 7 und 10 m/s ab. Durch diese schnelle und flexible Strahlablenkung können mehrere Lötstellen quasi simultan bearbeitet und komplexe Temperaturprofile erzeugt werden.
Die zum Löten erforderliche Temperatur an der Lötstelle entsteht dadurch, dass das Laserlicht auf die Oberfläche trifft, dort absorbiert wird und das Material erwärmt. Pad und Pin sind aus Metall. Sie sind temperaturstabil und haben einen geringen Absorptionsgrad, d.h nur wenig Lichtenergie wird in Wärme umgewandelt. Im Gegenteil dazu hat die umliegende Leiterplatte geringen Absorptionsgrad und eine deutlich geringere Temperaturstabilität. Trifft der Laserstrahl außerhalb des Pads die Leiterplatte, so kommt es zu Verbrennungen. Daher stellt das Laserlöten hohe Anforderungen an die Geometrie der Lötstelle und das Positioniersystem. Sind die Lagetoleranzen der Lötstellen zu groß, so müssen Positionsabweichungen durch den Einsatz von Bildverarbeitungssystemen kompensiert werden.
Das erforderliche Lot kann entweder während des Lötprozesses über einen Lotdrahtvorschub zugeführt oder vorab in Form von Paste, als Preform-Ring oder als Lotdepot auf die Lötstelle aufgebracht werden.
Der berührungslose Prozess minimiert Wartungsaufwand und Verschmutzung. Die Leistung der Laserdiode nimmt mit der Zeit ab, daher muss sie regelmäßig kontrolliert und angepasst werden. In der Regel hat eine Laserdiode eine Standzeit von 18-24 Monaten.
Ähnlich dem Laserlöten nutzt das Lichtlöten kurzwelliges Infrarotlicht (1µm) zur präzisen Wärmeeinbringung. Ein halbelliptischer Spiegel fokussiert die Strahlung in einem Brennpunkt, der auf die Lötstelle gerichtet wird. Der Brennfleckdurchmesser beträgt je nach System 2-3 mm. Im Gegensatz zum Laserlöten wird meist Lotpaste verwendet, was das Verfahren dem selektiven Reflowlöten ähnlich macht. Die geringere Energiedichte ermöglicht die Bearbeitung empfindlicher Substrate. IR-Strahler dienen oft auch zum Vorwärmen, um den Lötprozess zu beschleunigen.
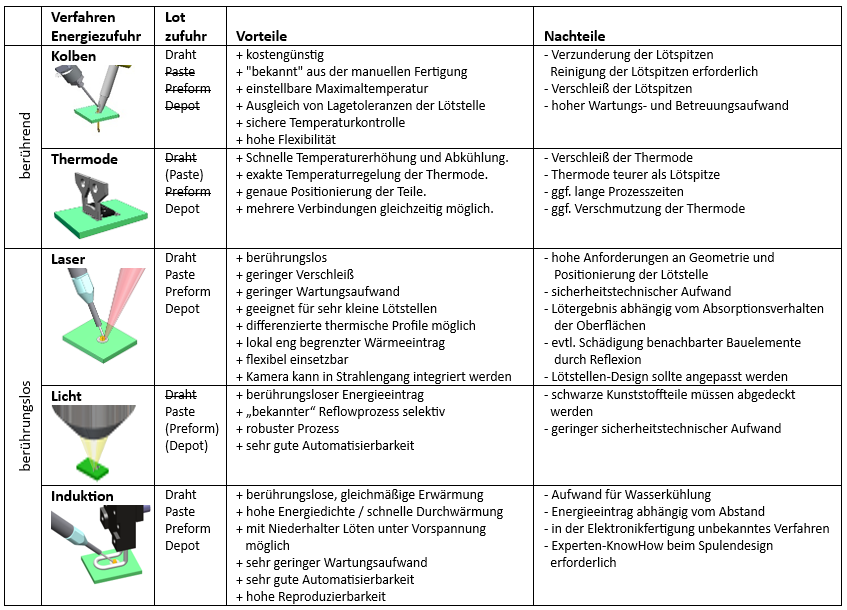
Induktionslöten
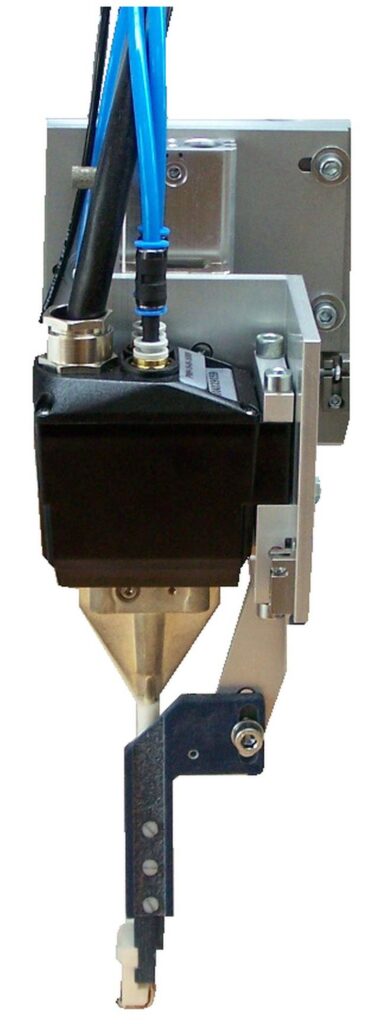
Beim Induktionslöten erzeugt ein hochfrequenter Strom in einer Sekundärspule ein Magnetfeld, welches Wirbelströme in den zu verbindenden Werkstücken induziert. Diese Wirbelströme erhitzen die Bauteile direkt an der Lötstelle, ohne den Induktor selbst zu erwärmen, was durch Kühlwasser im Spulendraht gewährleistet wird. Dieses Verfahren zeichnet sich durch hohe Energieeinkopplung und geringen Wartungsaufwand aus. Da die Energie nur in elektrisch leitende Materialien übergeht, eignet es sich besonders zum Löten auf temperaturempfindlichen Substraten wie Kunststoffen. Die hohe Energiedichte ermöglicht zudem löten von Bauteilen mit unterschiedlicher Wärmekapazität, beispielsweise massiver Pins auf dünnem Pad. Trotz seiner Vorteile ist Induktionslöten in der Elektronikfertigung noch selten anzutreffen, da Befürchtungen hinsichtlich einer Beschädigung elektronischer Bauteile durch das HF-Feld bestehen. Diese Bedenken sind unbegründet, da die induzierten Ströme zu gering sind, um Bauteile zu schädigen. Bei Anwendung in der Elektronik ist lediglich auf die Gestaltung der Masseflächen zu achten, um „Null-Ohm“-Schleifen und große Flächen in der Nähe der Lötstelle zu vermeiden. Scharfe Ecken sollten ebenfalls vermieden werden, da sie wie ein „Blitzableiter“ als Konzentratoren wirken können.
Für kleine THT-Lötstellen empfiehlt sich Verwendung von PreForm-Ringen, während bei größeren Lötstellen mit hohem Lotvolumen kostengünstigere Lotdrähte bevorzugt werden. Bei aufgelegten Kontakten hingegen verwendet man meistens Lotpaste oder Lotdepots. Die Induktionsspule muss auf die jeweilige Anwendung abgestimmt werden. Dabei ist zu berücksichtigen, dass Abstandstoleranzen zwischen Induktor und Prozessoberfläche die Erwärmung maßgeblich beeinflussen, da der Energieeintrag mit dem Abstandsquadrat abnimmt. Feldkonzentratoren und Ferriten können eingesetzt werden um die Feldverteilung zu optimieren.
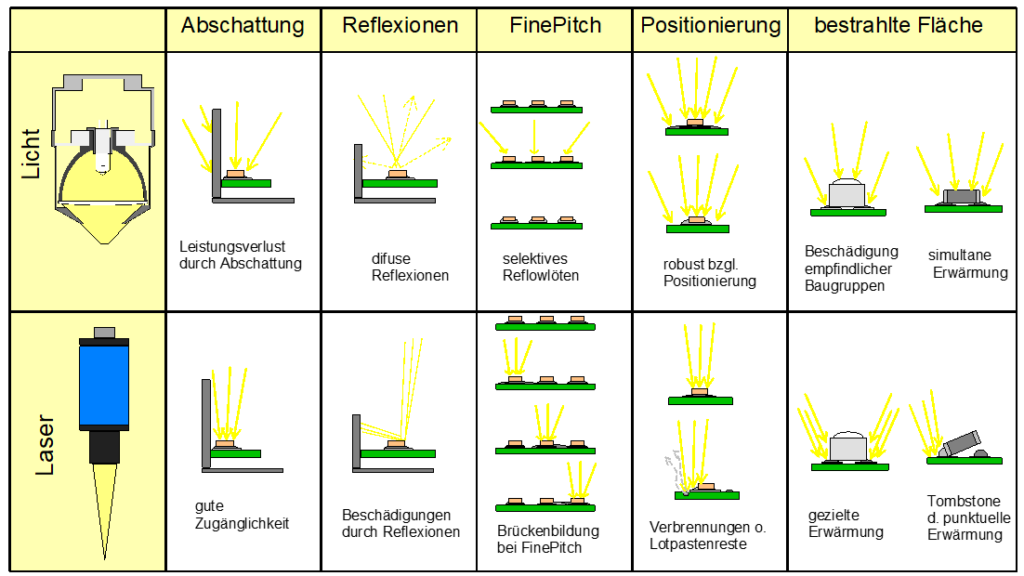
Thermodenlöten
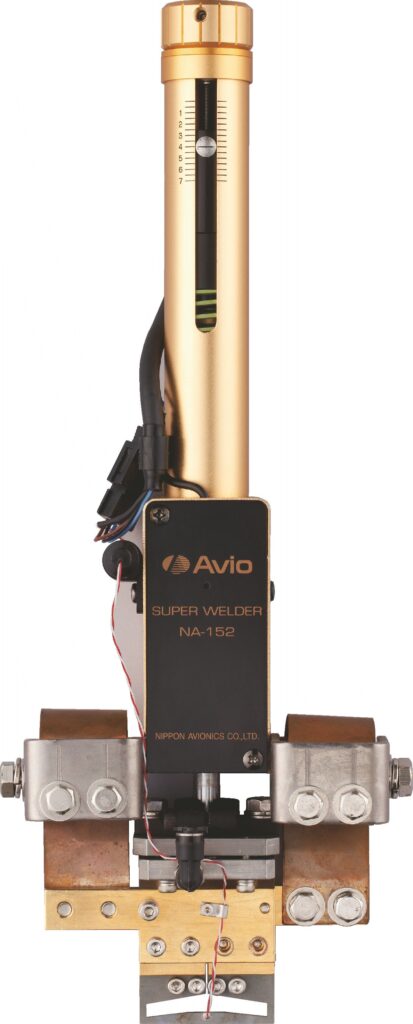
Im Gegensatz zu anderen Verfahren, die hauptsächlich bei THT-Lötstellen Anwendung finden, eignet sich das Thermodenlöten, auch Bügellöten oder Pulsheizverfahren genannt, speziell für das Löten von hochpoligen SMT-Bauelementen. Die Thermode ist so konzipiert, dass sie an der Lötstelle den geringsten Querschnitt und damit den höchsten elektrischen Widerstand aufweist. Dadurch heizt sie im Vergleich zum Lötkolben deutlich schneller auf und kühlt auch rascher wieder ab. Beim Thermodenlöten wird die Lötstelle mittels Thermode erhitzt, bis das Lot schmilzt. Anschließend wird die Stromzufuhr unterbrochen und die Thermode verbleibt auf der Lötstelle, bis das Lot erstarrt ist. So können auch unter Vorspannung stehende Kontakte, beispielsweise leicht verbogene, geebnet und gelötet werden. Der Prozess gliedert sich in vier Phasen: Antasten, Aufschmelzen, Nachsetzen und Abkühlen, deshalb zählt das Thermodenlöten nicht zu den schnellsten Lötverfahren. Um den Prozess zu beschleunigen, kann die Thermode gezielt mit Druckluft gekühlt werden. Die Lotzuführung erfolgt manchmal in Form von Lotpaste, meist aber durch Vorverzinnung der Fügepartner. Dann kann der Setzweg beim Aufschmelzen des Lotes als zusätzliche Prozesskontrolle detektiert werden. Typische Anwendungsgebiete für das Thermodenlöten sind löten von Flat-Packs, SMD-Stecker oder flexiblen Folien auf Leiterplatten.
Mikroflammlöten und Heißgaslöten
Beim Mikroflammlöten wird präzise Hitze von 2000-3000°C durch eine Wasserstoff-Sauerstoff Flamme erzeugt. Das Brenngas wird durch Elektrolyse gewonnen, dabei bestimmt die angelegte Spannung die Menge des erzeugten Gases. Doch diese Methode verliert an Bedeutung, da eine konstante Energiedichte und eine präzise Ausrichtung der Flamme schwer zu realisieren sind.
Daher wird das Verfahren häufig durch Induktionslöten ersetzt. Beim Heißgaslöten, auch Warmgaslöten oder Heißluftlöten genannt, wird heißes Gas, meist Luft, zur Lötstelle geleitet, hohe Temperaturen und Gasströme sind notwendig, bergen aber Gefahr der Überhitzung oder Verschiebung der Bauteile. Begrenzte Erwärmung ist mit Spezialdüsen möglich, die Umgebung erwärmt sich jedoch immer. In automatisierten Prozessen findet Heißgaslöten kaum Anwendung, da der Luftstrom vor Gebrauch erhitzt werden muss. In automatisierten Systemen wird Heißgas meist zum Vorwärmen verwendet, um den Lötprozess zu beschleunigen.
Dieser Beitrag wird im kommenden Heft mit dem Schwerpunkt auf die Auswahl des Lötverfahrens fortgesetzt.
ÜBER ATN
Die ATN Automatisierungstechnik Niemeier GmbH aus Berlin beschäftigt heute 40 Mitarbeiter und entwickelt, produziert und vertreibt seit mehr als 25 Jahren Komponenten, Systeme und Software für die
Elektronikfertigung. Dieses umfasst Löttechnik und Lötroboter sowie die komplette Dosiertechnik.