Yamaha Motor Europe N.V., Niederlassung Deutschland, Geschäftsbereich IM
Die Einführung der Roboterautomatisierung in einen etablierten Workflow kann kompliziert und teuer erscheinen. Mit der neuesten, modularen Technologie und intuitiven Setup-Tools können Unternehmen schnell und einfach mit der Nutzung der Vorteile beginnen und ihre Systeme skalieren und aktualisieren, wenn das Vertrauen gewachsen ist.
Industrielle Prozesse setzen zunehmend auf Automatisierung, um die Produktivitätsziele zu erreichen, indem sie so konstante Produktqualität und einen hohen Durchsatz sicherstellen. Ein Prozess kann vollständig automatisiert werden, frei von menschlichen Eingriffen oder teilautomatisiert sein, indem er die Stärken von Mitarbeitern und Maschinen verbindet.
Man stelle sich nur vor, wie Menschen und Maschinen im gleichen Raum kooperieren. Viele werden sich heute wahrscheinlich eine Reihe von multiartikulierten, kollaborativen Robotern („Cobots“) vorstellen, die programmiert sind, um die sich wiederholenden oder körperlich anstrengenden Aufgaben zu bewältigen. Die Mitarbeiter hingegen bringen ihre manuelle Geschicklichkeit oder kreative Inputs ein, die zur Vollendung des Prozesses erforderlich sind. Die Einführung von Robotern in eine Fabrik erfordert jedoch eine erhebliche Reorganisation der Prozesse und eine physische Umgestaltung des Arbeitsbereichs.
Auf der anderen Seite können Fertigungsunternehmen damit beginnen, die Vorteile der robotergestützten Prozessautomatisierung auf einfachere und weniger invasive Weise zu nutzen. Viele Produktionslinien sind mit Mitarbeitern besetzt, die Prozesse an Werkstücken durchführen, die von einem Transportsystem zu- und abgeführt werden (Bild 1). Eine Erhöhung der Transportgeschwindigkeit sollte die Werkstücke schneller zuführen und eine höhere Produktivität ermöglichen, aber oft ist das Gegenteil der Fall. Obwohl die Arbeiter physisch in der Lage sind, mit dem schnelleren Transport Schritt zu halten, können Probleme auftreten, da Werkstücke bei höheren Geschwindigkeiten Endanschläge erreichen und sich verschieben oder sogar auf den Boden fallen können. Durch die Erhöhung der Fördergeschwindigkeit kann die Produktivität sogar verringert werden.
Robotertechnologie trägt dazu bei, dieses Problem zu lösen. Linearroboter können herkömmliche Transportsysteme ersetzen, sind einfacher zu programmieren und verfügen über digital definierte Start- und Stopppositionen ohne mechanische Endanschläge. Beschleunigung und Verzögerung erfolgen fließend innerhalb vordefinierter Entfernungen und ermöglichen kurze Transportzeiten. Mehrere dieser Module können unabhängig voneinander an derselben Produktionslinie betrieben werden, um ein einziges, mit durchgehend gleicher, konstanter Geschwindigkeit betriebenes Transportsystem zu ersetzen. Dies gibt die Flexibilität, die Transportgeschwindigkeit in mehreren Zonen entlang der Linie separat zu optimieren, um den Anforderungen jedes Teilprozesses gerecht zu werden und die Arbeitsabläufe auszubalancieren.
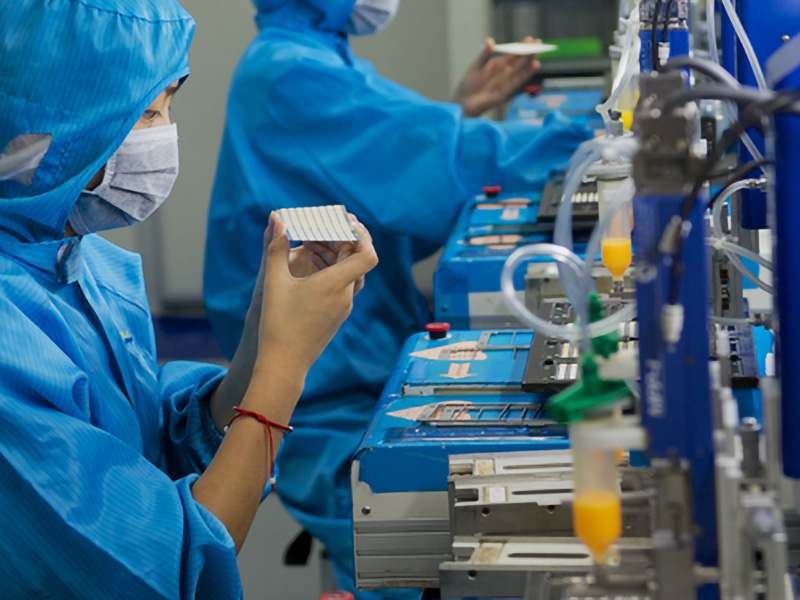
Darüber hinaus eröffnet die Flexibilität, in Vorwärts- und Rückwärtsrichtung zu transportieren, neue Möglichkeiten, noch mehr Effizienz zu erzielen. Yamaha hat es mehreren Kunden ermöglicht, diese Vorteile zu nutzen, indem sie Yamahas robotergestütztes Linearfördermodul LCMR200 (Bild 2) in Produktionslinien integriert haben. Dieses Modell ist schnell, effizient und auch weniger anspruchsvoll bei der Reorganisation von Arbeitsabläufen als die Einrichtung von mehrachsigen Gelenkarm-Robotern.
Dieser modulare, lineare Roboter kann einen bequemen Einstieg in das Potenzial der Roboter-Prozessautomatisierung bieten, das vom einfachen Austausch eines Förderbandes oder Rundschalttisches bis hin zur vollständigen End-to-End-Prozessautomatisierung in einer geschützten Roboter-Montagezelle reichen kann.
Wenn es darum geht, einen kompletten, robotergestützten automatisierten Prozessablauf für den Bau kleiner Produkte wie Lautsprecher oder Automobilmodule mit mehreren Einzelteilen zu schaffen, müssen Lösungsintegratoren oft Roboter verschiedener Typen kombinieren, um alle einzelnen Montagearbeiten kostengünstig und platzsparend durchzuführen. Yamaha verfügt über eine einzigartig umfassende Auswahl an Industrierobotern aller gängigen Typen, vom modularen LCMR200 und anderen einachsigen Robotern bis hin zu kartesischen und SCARA-Robotern. Diese bieten Lösungsintegratoren alle benötigten Optionen, um auch bei beengten Platzverhältnissen in der Fertigung einen effizienten Workflow zu schaffen und gleichzeitig wichtige Aspekte wie Wartbarkeit, Programmierbarkeit und Benutzerfreundlichkeit zu berücksichtigen.
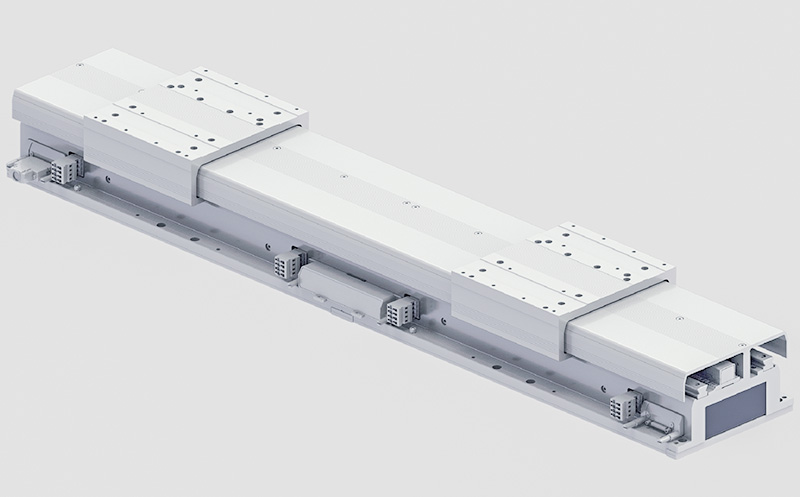
Es gibt viele platzsparende Aspekte der Yamaha-Roboterlinie, wie z. B. die deckenmontierte, Orbit-Serie YK-TW der SCARA-Roboter, die eine Unterfahrbewegung ermöglicht, bei der die Greiferspitze unter der Haupteinheit durchfahren kann (Bild 3). Das Erreichen eines kompakten Prozess-Footprints kann äußerst wichtig sein, z. B. für OEMs, die ein „Re-shore“ anstreben oder früher ausgelagerte Prozesse wieder unter interne Kontrolle bringen wollen. Obwohl globale wirtschaftliche Veränderungen bedeuten können, dass Re-shoring finanziell sinnvoll ist, verfügt die lokale Fabrik oft über sehr wenig freie Flächen für die Aufnahme der zurückkehrenden Prozesse. Wo jeder Quadratzentimeter wertvoll ist, haben SCARA-Roboter vom Typ Orbit gezeigt, dass sie auf engstem Raum arbeiten können. Mit 350 mm Armlänge und 5 kg Nutzlast kann eine Einbaubreite von nur 492 mm erreicht werden.
Die Hauptstärken der SCARA-Roboter liegen in der schnellen Entnahme und Bewegung von Werkstücken sowie in der Durchführung von Montageprozessen wie dem Einschrauben von Schrauben und dem präzisen Dosieren von Klebstoffen, Dichtstoffen oder Wärmeleit-Materialien. Die typischen Größen der SCARA-Roboter reichen von einer Armlänge von 120 mm bei einer Nutzlast von ca. 1 kg bis hin zu
1200 mm-Modellen, die bis zu 50 kg aufnehmen können. Die YK-XG-Familie von Yamaha verwendet wartungsfreie, riemenlose Antriebe, die eine schnelle und hochpräzise Bewegung in vier Achsen ermöglichen. Darüber hinaus wurde das Trägheitsmoment optimiert, um eine schnelle Drehung schwerer Objekte zu ermöglichen, bei denen herkömmliche Maschinen ihre Geschwindigkeit reduzieren müssen, was zu längeren Taktzeiten führt.
Yamaha profitiert von seiner langjährigen Erfahrung, die von frühen Industrierobotern herrührt, die in den 1970-er Jahren zur Automatisierung der Montage von Motorradteilen in großen Stückzahlen entwickelt wurden. Später hat Yamaha seine Roboter mit innovativen Funktionen wie dem TRANSERVO ausgerüstet, die es Schrittmotoren ermöglichen, sowohl hohe Geschwindigkeiten, als auch hohe Drehmomente zu liefern.
Weitere Merkmale, die Integratoren schätzen, um die Herausforderungen bei der Lösungskonzeption zu vereinfachen, sind wartungsarme Schmierung und effektive Schadstoffbarrieren, innovative, hochfeste mechanische Teile, die auch bei hohen Presskräften eine außergewöhnliche Genauigkeit gewährleisten und der weit verbreitete Einsatz von Positionsresolvern, die robuster und zuverlässiger sind, als herkömmliche, optische Positionsgeber.
Mit einer Vielzahl von Steuerungssystemen zur Auswahl, können Integratoren eine kostengünstige Lösung konfigurieren, um die Herausforderungen der Automatisierung zu bewältigen und gleichzeitig den Weg für zukünftige Anpassungen und Skalierungen offen zu halten. Einfache Steuereinheiten für die Basispositionierung und den Antrieb ermöglichen die einfache Steuerung von Einachsrobotern mit Koordinatenanzeige oder Impulszug-Eingabe, um die Programmierung zu minimieren. Auf der anderen Seite können Mehrachsen-Controller verwendet werden, um einen oder mehrere Ein- oder Zweiachsenroboter gleichzeitig zu steuern. Bis zu vier 4-Achsen-Steuerungen können in Master-Slave-Konfiguration verknüpft werden, um max. 16 Achsen zu verwalten und die Steuerung in einem Programm zu konsolidieren, das in der Robotersprache von Yamaha (erweiterte Version von BASIC) geschrieben ist.
Hochrüstung nach erfolgter Vertrauensbildung
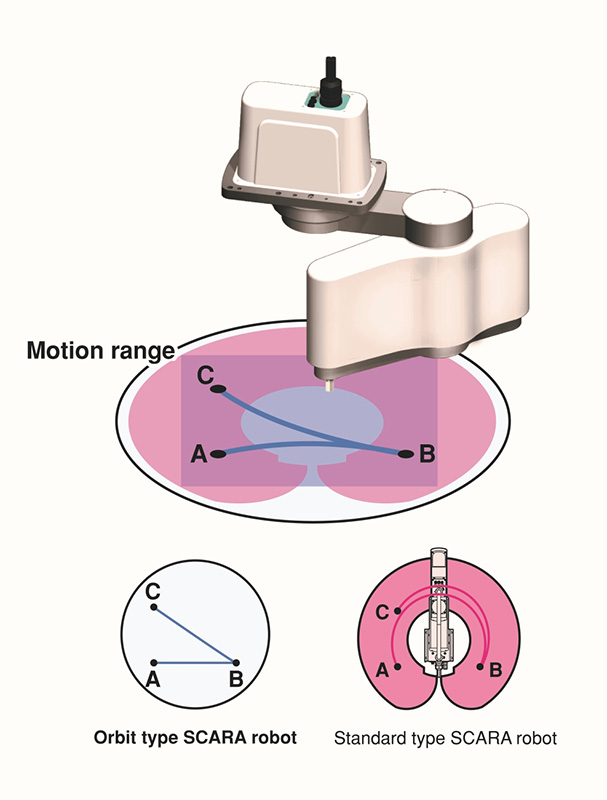
Der Erfolg in einem ersten Automatisierungsprojekt ermutigt Betreiber oft, ihre Systeme zu skalieren oder zu erweitern, um eine höhere Produktivität oder End-of-Line-Qualität zu erreichen. Die Einführung der industriellen Bildverarbeitung ist eine beliebte Art der Hochrüstung, obwohl die Technologie typischerweise Spezialwissen und umfangreiche Einrichtungsprozesse erfordert, die kompliziert und zeitaufwändig sein können. Zu den häufig anzutreffenden Herausforderungen gehört die Einrichtung der Kommunikation zwischen dem Bildverarbeitungssystem, dem Roboter und anderen Subsystemen wie z. B. dem Transport-Nachverfolgungssystem. Weitere Hürden sind die Kalibrierung des Bildverarbeitungssystems und die Gewährleistung einer genauen Registrierung der Werkstückdaten.
Yamaha hat sich bei der Entwicklung seines RCXiVY2+-Systems zum Ziel gesetzt, die Roboter-Bildverarbeitung zu vereinfachen. In einem typischen Roboter-Vision-System sind die Kameras an einen dedizierten Bildverarbeitungs-Prozessor angeschlossen, der dann über eine serielle Datenverbindung mit der Hauptsystem-Steuerung kommuniziert. Im RCXiVY2+-System werden die Bildverarbeitung, die Beleuchtungssteuerung und die Verarbeitung der Daten des Transport-Nachverfolgungssystems innerhalb des Roboterprogramms unter Verwendung spezieller Bildverarbeitungsbefehle abgewickelt, die von Yamaha erstellt und dem erweiterten BASIC-Befehlssatz hinzugefügt wurden. Der Vision-Befehlssatz vereinfacht die Komponentensuche und -verfolgung und reduziert die Suchzeiten um bis zu 50 Prozent. Eine schnellere Suche verbessert die Teileerkennung bei hohen Transportgeschwindigkeiten und ermöglicht eine effiziente Teileaufnahme sowie geringere Taktzeiten.
Mit der Hardware, darunter ein Vision-Board mit GigE-Kameraschnittstelle, ein Beleuchtungssteuerungs-Board und ein Tracking-Board, die alle einfach direkt in die Mehrachsen-Robotersteuerung der RCX3-Serie eingebaut werden, werden viele Integrationsprobleme umgangen und die Kompatibilität mit Peripheriegeräten ist gewährleistet. Da die Bildverarbeitung durch das Roboterprogramm verwaltet wird, ist es darüber hinaus nicht erforderlich, eine Routine zur Koordinatenkonvertierung zu erstellen. Darüber hinaus steigert das integrierte System von Yamaha die Leistung, indem es die Verzögerungen eliminiert, die bei der herkömmlichen Bildverarbeitung auftreten, da dort die Kameradaten einen separaten Vision-Prozessor durchlaufen und dann erst an die Robotersteuerung weitergeleitet werden.
Um die Einrichtung des Systems zu beschleunigen, hilft ein einfacher, von einem Assistenten unterstützter Kalibrierungsprozess, die Kamerakoordinaten schnell auszurichten. Ein grafisches Tool reduziert die Werkstückregistrierung auf drei einfache Schritte, indem es bei der Bilderfassung, der Einstellung der Kontur und der Registrierung der Erfassungsposition unterstützt. Insgesamt ist die Einrichtungszeit um etwa 80 Prozent kürzer als bei einem herkömmlichen Machine-Vision-System.
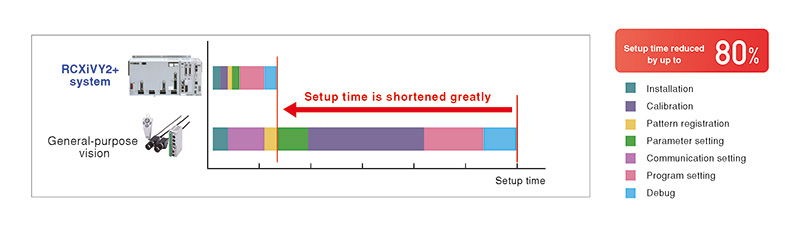
Im Einsatz verbessert eine leistungsstarke Bildkanten-Suchmaschine die Teileerkennung. Das System kann Schrauben und Unterlegscheiben erkennen, die Teile befestigen, Gegenstände in einer Verpackung oder auf einer Leiterplatte erkennen, Bohrlöcher überprüfen und Objekte wie Flaschen in einer Palette oder elektronische Bauteile zählen. Über den DVI-I-Ausgang der Kamera können Anwender den Suchstatus jederzeit analysieren und bis zu 254 zusätzliche, benutzerdefinierte Teile für die automatische Erkennung registrieren. RCXiVY2+-Kameras können an festen Positionen über und/oder unter dem Werkstück oder am Roboter montiert werden. Wenn die Kamera am Roboter montiert ist, werden die Kamerakoordinaten automatisch entsprechend der Bewegung korrigiert.
Das RCXiVY2+-System führt auch einen neuen Ansatz zur Bildverarbeitung ein, die so genannte „Blob-Erkennung“, die Objekte mit unregelmäßigen Formen bis zu 10-mal schneller als herkömmliche Kantenerkennungsmethoden identifizieren kann. Sie verbessert die Teileaufnahme, die Anwesenheitserkennung und das Hochgeschwindigkeitszählen von mehreren Werkstücken und ist besonders effektiv bei Artikeln wie Lebensmitteln und Kleidung, wodurch das mögliche Anwendungsspektrum für die Roboter-Bildverarbeitung erweitert wird. Das System kann auch durch Überlappungen teilweise verdeckte Teile erkennen und diese gezielt aus der Suche ausschließen.
Fazit
Herkömmliche manuelle Montageprozesse, auch wenn sie durch Basisautomatisierung wie motorgetriebene Transportsysteme unterstützt werden, bieten nur begrenzte Möglichkeiten zur Steigerung von Durchsatz und Produktivität. Typische Ansätze zur Verbesserung der Taktzeit können oft einen gegenteiligen Effekt auf die Produktivität haben. Erforderliche, weitere Mitarbeiter und zusätzliche Produktionslinien erhöhen die Betriebskosten und erfordern mehr Produktionsfläche.
Der Einstieg in die robotergestützte Prozessautomatisierung kann einfach und unterbrechungsfrei sein, wenn sie richtig angegangen wird, z. B. durch den Austausch unflexibler Förderbänder oder platzraubender Rundschalttische durch programmierbare Linearroboter. Wenn das Vertrauen wächst, kann die Automatisierung auf andere Prozesse und Produktionslinien ausgedehnt werden und es können Hochrüstungen wie die Bildverarbeitung hinzugefügt werden, die einen immer schnelleren Return-on-Investment ermöglichen.