Die Brennstoffzelle gilt als die Zukunft. Die Zukunft der Automobilindustrie, der Gebäudetechnik, der Luftfahrt, der Schwerindustrie und unzähliger weiterer Branchen. Die Reaktion von Wasserstoff und Sauerstoff in einer galvanischen Zelle verspricht einen einzigartig ökologischen, transportablen und speicherbaren Umgang mit elektrischer Energie. Neun Milliarden Euro will die Bundesregierung in die Technologie investieren, unter anderem, um bis 2030 einen Wasserstoffbedarf von 90 bis 110 TWh zu decken – eine Energiemenge in der Größenordnung des jährlichen Verbrauchs von rund 14 Millionen Menschen und damit von über 80 Prozent der Einwohner von Nordrhein-Westfalen.
Um die gesetzten Klima-Ziele zu erfüllen, werden nicht nur in der Zukunft, sondern schon heute qualitativ hochwertige Brennstoffzellen-Komponenten in skalierbarer Fertigung benötigt – Komponenten, wie sie mit den Maschinen der MASS GmbH aus Geseke in Nordrhein-Westfalen entstehen. „Egal, welche Substrate in den Brennstoffzellen der Gegenwart oder Zukunft zum Einsatz kommen, ob brennbar oder nicht-brennbar, organisch oder anorganisch, viel oder wenig Lösemittel: Wir können sie weiterverarbeiten“, beschreibt Geschäftsführer Jürgen Resch die aktuellen Herausforderungen. Sein Unternehmen bietet mit der Neuentwicklung MASS MT 400 Eta-Line eine maßgeschneiderte Lösung für die Trocknung von Siebdruckpasten, wie sie in der Membran-Elektroden-Einheit einer Brennstoffzelle zum Einsatz kommen sowie in deren mikroelektronischen Bauteilen.
Die Zelle der Zukunft:
Kundenindividuelle Lösungen zur Trocknung in Magazinen
„Unser neuestes Produkt aus der MT-Serie ist speziell für die Trocknung von Brennstoffzellen in Magazinen nach dem Bedrucken entwickelt worden“, so Resch weiter. Eine moderne Brennstoffzelle für den mobilen Betrieb besteht in der Regel aus einer Elektrolytmembran, die von zwei Elektroden umgeben ist. An der Anode wird zugeführter Wasserstoff in Elektronen und Protonen aufgeteilt. Lediglich die Protonen können durch die Polymermembran direkt zur Kathode gelangen, wo sie mit den durch den Stromverbraucher geleiteten Elektronen und Luftsauerstoff zu Wasserdampf reduzieren. Unter anderem aufgrund der brennbaren und potentiell explosiven Kombination von Wasserstoff und Sauerstoff sowie der anvisierten langfristigen Nutzungsfelder stellt die Praxis hohe Anforderungen an die Komponentenqualität von Brennstoffzellen. Von entscheidender Bedeutung hierfür ist die maßgeschneiderte Aushärtung der Siebdruckpasten nach der Bedruckung. Für diesen Prozessschritt liefert die MASS GmbH bereits seit mehr als dreißig Jahren Sondermaschinen in kundenspezifischer Fertigung und bietet mit dem MASS MT 400 Eta-Line nun noch eine Steigerung hinsichtlich der Anpassbarkeit: Das komplette System ist mit seinen acht Heizzonen und zwei Kühlzonen modular aufgebaut und bietet dem Kunden in jedem Fertigungsschritt die exakt benötigten Bedingungen hinsichtlich Temperatur, Standzeit oder ATEX-Konformität. „Somit ist jede der Zonen eigenständig zu betrachten und der Kunde zahlt am Ende nur für die Elemente und Eigenschaften, die auch in dem jeweiligen Prozessschritt benötigt werden“, so Konstrukteur Stephan Ulrich Ströhmeier.
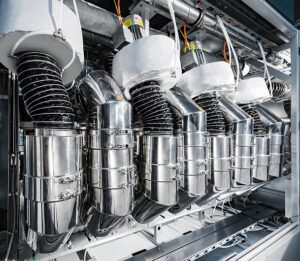
MASS MT 400 Eta-Line – Die neue MASS Ofen-Generation für Erwärmung und Trocknung in industriellen Fertigungsprozessen
Das neu entwickelte Regelungskonzept kann prozessspezifisch die jeweils passenden Regelparameter selektiv einstellen und so mit einem möglichst geringen Energieaufwand ein optimales Ergebnis erzielen. Die Parameter können für jede der acht Heizzonen einzeln justiert werden, ebenso wie die Be- und Entlüftung hinsichtlich ATEX-Konformität. In dem vorliegenden Explosionsschutz-Konzept des MT 400 Eta-Line wurden die sicherheitstechnischen Kenngrößen aus den Kundenanforderungen in ein individuelles maschinentechnisches und betriebliches Sicherheitskonzept übertragen.
Die bei Brennstoffzellen in der Regel verwendeten Substrate lassen sich optimalerweise in Magazinen transportieren, lagern – und somit auch trocknen. Dies wirkt sich bei der MASS MT 400 Eta-Line zugleich positiv auf die Profitabilität aus, da sich eine große Anzahl an bedruckten Substraten bei gleichzeitig minimalem Platzbedarf und geringem Energieaufwand trocknen lassen. Die Modulbauweise ermöglicht jede kundenspezifische Modifizierung und kann an die jeweils benötigte Taktzeit angepasst werden. Die Heizregister garantieren ein sehr eng toleriertes Quer- und Höhenprofil, während die Heizzonenanzahl je nach gefordertem Temperaturprofil modular ausgelegt wird – die neuste Generation der MT-Serie ermöglicht somit präzise Stufenprofile.
Nachhaltig in jedem Prozessschritt
mit intelligenter Wärmedämmung und Wärmenutzung
Zudem ermöglicht der modulare Aufbau auch eine nahezu unbegrenzte Skalierbarkeit: „Für die geplante Zukunft der Wasserstoff-Technologie werden große Mengen an Brennstoffzellen und den jeweiligen Komponenten benötigt – mit unseren Produkten können unsere Kunden bequem mit der Entwicklung mitwachsen“, beschreibt Ströhmeier die Vorteile des modularen Aufbaus. Gleichzeitig gilt es auch diesen Prozessschritt in der Fertigung möglichst nachhaltig zu gestalten, um den ökologischen Fußabdruck der Produktion gering zu halten. Die MASS MT 400 Eta-Line setzt auf Wärmerückgewinnung. Zudem bewirkt die Bauweise mit einem innenliegenden Rahmenprofil und einer aufliegenden Außenverkleidung eine maximierte Wärmedämmung, sodass der Energieaufwand für die Erzeugung der Konvektionswärme mit Temperaturen von bis zu 200° Celsius minimiert wird.
Die pro Prozessschritt vorgeschriebenen Temperaturen werden – gegebenenfalls nach computergestützter Optimierung – auf bis zu zwei Prozent pro 100° Celsius genau eingehalten und in jeder Trocknungsphase hinsichtlich der Prozesstemperaturen und Prozesszeiten lokal in der Anlagensteuerung oder remote im Produktionsleitsystem (MES-System) dokumentiert. Nur Produkte mit Trocknungstemperaturen innerhalb der definierten Korridore werden gutgeschrieben, andernfalls für Folgeprozesse als gesperrt klassifiziert. Am Ein- und Auslauf ist ein modernes Lesegerät integriert, der eine lokale und dezentrale Nachverfolgung der Produkte ermöglicht. An diesen Stellen bietet das System zudem die Verwaltung der Ofenprofile für eine flexible Prozessgestaltung.
Die Wasserstoff-Brennstoffzelle soll der Wirtschaft und der Gesellschaft eine dringend benötigte Flexibilität und Sicherheit bei der Speicherung und mobilen Nutzung von regenerativen Energien bieten – und erfordert diese wiederum in jedem Prozessschritt der Fertigung. Skalierbarkeit, Anpassbarkeit und Prozesssicherheit werden wichtige Messgrößen in der Phase der flächendeckenden Etablierung der neuen Technologie, wie vergangene Paradigmenwechsel in technologischen Bereichen gezeigt haben. Oder um es mit den Worten von Jürgen Resch zu sagen: „Egal, welche Substrate in den Brennstoffzellen der Gegenwart oder Zukunft zum Einsatz kommen – wir können sie sicher weiterverarbeiten.“
Über die MASS GmbH
Die MASS GmbH entwickelt und produziert Beschichtungs- und Erwärmungsanlagen sowie Trockner und Handlings-Geräte für die Leiterplatten-, Mikroelektronik- und Solarzellenindustrie. Durch mehr als 30 Jahre ständig wachsendes Know-how und die konsequente Weiterentwicklung des hohen technischen Standards sind Gießanlagen, Trockner und Handlinganlagen Bestandteil eines geschlossenen Lieferspektrums.